WP: How to achieve 400 UPH with Locus Fast Pick
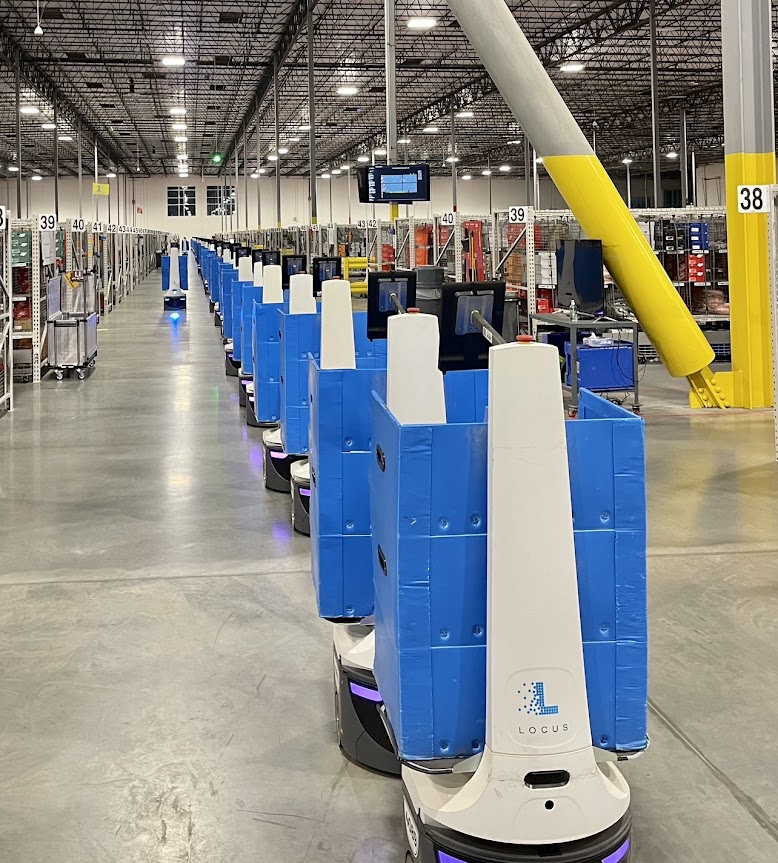
Overview & Challenge
Bluegrass Supply Chain is a third-party logistics (3PL) provider based in Bowling Green, KY. Founded in 2002, they strive to deliver innovative solutions to make their customers and their supply chains better. Serving primarily automotive, food and beverage, and consumer goods companies, Bluegrass provides value added fulfillment, Just-in-Time/Just-in-Sequence, cross docking, ecommerce fulfillment, light assembly, and engineering support services over a five-state region.
The team at Bluegrass Supply Chain has witnessed remarkable results after integrating autonomous mobile robots (AMRs) from Locus Robotics into their operations.
Improved Efficiency
AMRs have revolutionized the Bluegrass workflow, setting the pace for their team members. Their robots take the most efficient path and proactively alert the team to delays.
With the AMRs, Bluegrass has seen a 200% increase in picking efficiency. In fact, the time to get a picker to pick at rate has been reduced from two weeks to two hours since introducing AMRs! The robots allow pickers to work hands-free and keep their processes running smoothly, allowing Bluegrass to handle orders more quickly and effectively.
Reduced Errors
The use of AMRs has significantly reduced the chance of human errors in order picking and inventory management.